The evolving needs of the process industry
Industrial Ethernet is the answer to the question of how to obtain reliable connectivity. With Ethernet-APL and Single Pair Ethernet, seamless data communication becomes possible, even in the most challenging environments, ensuring reliability. By adopting Industrial Ethernet, you gain real-time data access and furthermore improve system interoperability. Up to now, many process plants struggle with missing standards of process values and asset data. This is why open digital communication is crucial, especially because asset data like firmware, configuration files, and diagnostics support the scalability of your business. Smart Ethernet devices, powered by protocols like PROFINET, Modbus TCP, EtherNet/IP and Ethernet-APL enable seamless communication, making automation more efficient and scalable. As industries move toward digitalization, Ethernet-based networks lay the foundation for smarter, more connected, and future-ready operations.
The emergence of Ethernet-based communication protocols
Not so long ago, the potential of Ethernet started to gain attention as a physical layer for field level integration in industrial applications. As the backbone of modern connectivity, Ethernet enables high-speed and low-latency data transmission, seamless system integration, as well as minimal-error, reliable remote access - essential for today’s smart manufacturing environments.
In the food and beverage industry, Ethernet-based protocols are commonly used. These protocols help in maintaining the quality and consistency of products by enabling precise control over production processes. The chemicals industry also benefits from Ethernet-based protocols, which facilitate the integration of complex chemical processing equipment, ensuring accurate data transmission and control. In the life sciences sector, Ethernet-based protocols are used to manage sophisticated laboratory equipment and automated systems. These protocols enable seamless communication between various devices, ensuring that experiments and processes are conducted with high precision and reliability. PROFINET's real-time capabilities are particularly valuable for applications requiring stringent control and monitoring.
Beyond performance and interoperability, Ethernet-based communication also drives cost-efficiency by reducing cabling requirements, minimizing labor needs, and optimizing resource usage. It plays a key role in enhancing safety and ensuring compliance, with real-time monitoring of hazardous conditions and the automation of safety protocols. These capabilities not only protect your personnel and your equipment, but also support adherence to industry regulations through accurate data tracking and reporting.
Ethernet-APL: Enhancing connectivity and efficiency
Do you want to combine Ethernet’s speed with your specific demands for process automation? Ethernet-APL (Advanced Physical Layer) is the answer – providing fast and secure data transmission even in hazardous industrial environments. Ethernet-APL takes digitalization even further, supporting full end-to-end connectivity throughout the entire process plant lifecycle.
For a long time, there has been a lack of standardization across industrial infrastructure. According to the 2024 Industrial Network Report issued by Cisco, up to 37% of the industry mentions this as one of the major concerns. That is one of several reasons why the leading standards organizations worked together with major industry partners like Endress+Hauser to specify an Advanced Physical Layer for Ethernet that meets the requirements of process industries. Ethernet-APL is designed to be open, future-proof and ready for the Industrial Internet of Things (IIoT). In the same study, 63% of respondents mentioned that they had increased their spending on infrastructure, with 28% betting on Ethernet to future-proof their operations already now.
After analogue communication was innovated by fieldbus technology, we are now heading to the next level of industrial communication. With its speed, robustness and interoperability, Ethernet-APL overcomes previous limitations and offers a whole new approach to field connectivity. Fully compatible with leading protocols like PROFINET and EtherNet/IP, Ethernet-APL is future-proven and driving the evolvement of industrial automation in different sectors. For example:

IO-Link: Transforming device connectivity
The standardized communication protocol improves connectivity by offering seamless interoperability, offline parameterization, and real-time diagnostics. IO-Link allows for remote configuration and monitoring of devices, enhancing operational flexibility and reducing the need for manual adjustments.
In addition, IO-Link's ability to integrate with various fieldbus systems makes it ideal for upgrading existing setups with modern automation technologies, especially where the process environments and requirements of the instruments are rather simple. As a complementary option to ethernet-based structures, IO-Link is a perfect fit for measurement points that can be described as less critical.
How IO-Link supports different industries

Explore the benefits of IO-Link for industrial automation
Throughout the lifecycle of a plant or a skid, the equipment must meet stringent demands: easy installation, efficient operation and intelligent optimization. For these challenges, digitalization through IO-Link offers solid solutions. Do you have a variety of measuring device providers in your plant? IO-Link works across manufacturers, ensuring reliable sensor and actuator communication.
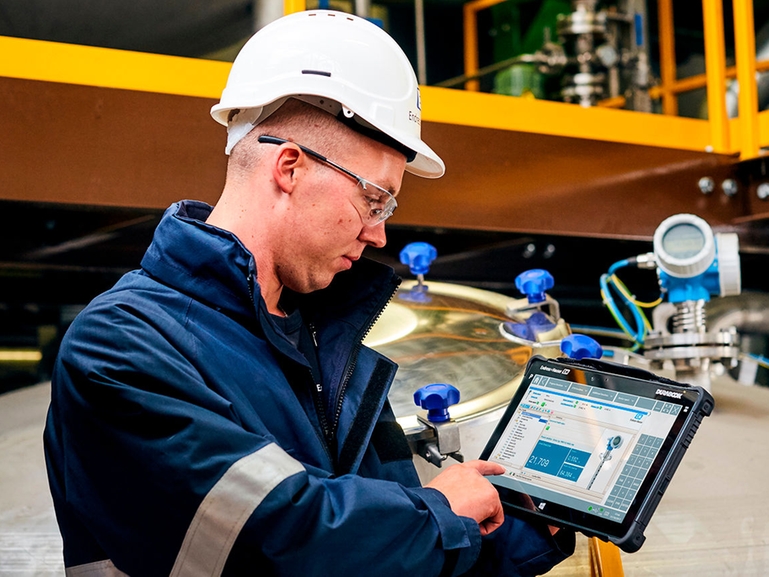
Rely on our support to validate and commission your digital networks
In a situation where a customers construct a new facility or adapt the network of an existing plant, it is crucial to check the digital communication options make a solid decision. With our expertise in designing and commissioning digital networks, we can support you during this process. We offer a service for validating and commissioning network topologies to ensure that our customers implement the best possible technology for their individual use case.
Find out more on how our consultancy and commissioning service can help you by downloading our application information.